3D printing to touch
For quality assurance in 3D printing with mixed reality app, Hololens and point cloud - researchers at the FHV's HCT Research Centre are advancing integrated quality assurance in FDM 3D printing.
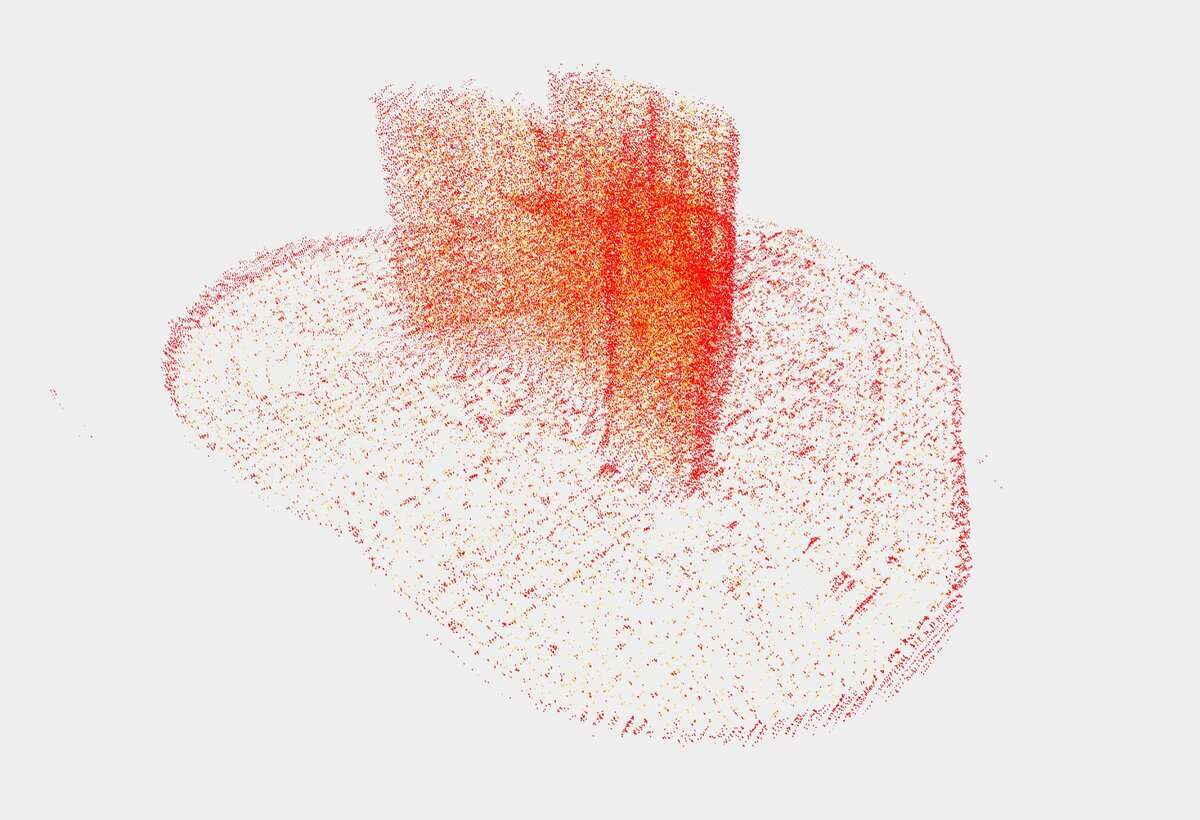
On quality assurance in 3D printing with mixed reality application, Hololens and point cloud.
Researchers at the HCT Research Centre at the Vorarlberg University of Applied Sciences (UAS) are further developing integrated quality assurance in FDM 3D printing (previously described here). Using a mixed reality (MR) application developed at the FHV, data from a 3D print recorded by a laser scanner is displayed on Microsoft HoloLens 2 MR glasses. The data used by the application includes the points recorded by the laser scanner in three-dimensional space, as well as the distance of each point from the target model. The MR application processes this information into a color-coded point cloud in three-dimensional space. The point cloud can be blended over the 3D print directly in the print space using a marker.
660,000 points highlight print defects in color
The MR application was developed using the Unity game engine. The AR library Vuforia is used to place the model in real space. The prepared CSV data can be read from the glasses or a network drive. Subsequently, the data is processed on the HoloLens and displayed as a color-coded point cloud. The color coding results from the distance of the points from the target model, so the points are colored from green (0.0mm) to red (≥0.2mm) depending on their deviation from the target model. To highlight defects in the print, the points are displayed from green to red with increasing opacity. Since these are dense point clouds (about 660,000 points for a 1.2cm 3D print) and processing the data into a 3D model happens directly on the HoloLens, performance was the biggest challenge. To render the point cloud on the HoloLens 2, a mesh is created that includes a vertex at the appropriate location for each point. A self-programmed shader renders a triangle at each vertex that always aligns with the glasses. Each vertex can have an arbitrary color, which is rendered accordingly by the shader.
Two mechanisms for vertex reduction
To further improve performance, two point reduction mechanisms have been implemented. The first mechanism discards points depending on their distance from the target model with a certain probability. Thus, points with a small deviation are only considered with a 20% probability, while points with increasing deviation are represented with a higher probability (up to 100%). This results in the elimination of approximately 360,000 points in the 660,000 point model used. The second mechanism takes into account the layer thickness as well as the height of the currently printed layer. After a layer has been printed, the laser scanner moves over the model and saves the data in a new file. Thus, a separate CSV file with points is available for each layer. Since the laser scanner scans a larger area, underlying points that were already taken into account in previous layers are also scanned. For each layer, the MR application only takes into account the points that were scanned at this height and the points that are within a configurable tolerance range. For points with a particularly large deviation, an extended tolerance range can be defined in order to reliably map print errors. As a result, in the model used, which comprises 660,000 points with a defined tolerance range of four layers up and down in each case and an extended tolerance range of a total of eight layers up and down in each case, approx. 130,000 points can be eliminated for points with a particularly large deviation. Thus, by applying these two mechanisms, only about 170,000 points of the 660,000 were taken into account.
In the images, the superimposition of the point cloud over the real 3D print is visible through the HoloLens 2. A menu can be used to configure the display; for example, it is possible to scale the model, as can be seen in the second image.
Contact
January 2022